BMW DCT related links
•BMW DCT BIG HOWTO. <-- READ this guide, please, just do it before asking questions already covered.
•BMW DCT error codes.
•BMW DCT TCU firmware flashing.
•BMW DCT CAN protocol.
•BMW INPA diagnostic tool.
•DCT clutch relearn.
•DCT hardware identifier
•DCT hardware upgrade.
•BMW installation and wiring.
•DCT shifter emulation.
•DCT Realtime Data description.
•DCT shifting options.
•MTune - DCT Control.
•MTune - DCT Settings.
How does the BMW TCU torque control works
(even more information here for the gecky customers...)
•All torque values transmitted to the TCU is between -1024 and 1023Nm.
•The transmitted torque value has a direct relation to the DCT clutch pressures, but be aware, DO NOT send to much torque to the TCU on lower loads (since that will not give you a smooth shift transition).
•If you engine produces max 600Nm on the dyno, there is no reason to send 1000Nm if you do not want to make sure you have maximum clutch pressure, always keep an eye on the RealTime Data Value clutch slip.
•The standard torque table values will probably work for most setup, but might require a little bit of tweaking.
•The torque strategy transmitted to the TCU is HIGHLY advanced, but we have tried to simplify everything to make it easier for you to tune in, therefore, only one torque value is available to be tuned.
•The shifting operation uses the pedal position (drivers torque choice) and the SPORT (GEN1 335) button / Drivelogic mode 1-6 (GEN1 M3) / Drivelogic mode 1-3 (GEN2) as a simplified and automatic shift hardness setting. GEN1 Mode 6 / GEN2 Mode 3 + full throttle = maximum shift hardness
clutchslip mode during launch
When enabled, we will not transmit the brake signal to the TCU, and you can use this method to "build boost against the clutch", over a VERY short period of time before you eventually will burn them. <-- DO NOT blame us if you end up with damaged clutches, you have been warned.
Example usage of the torque during launch table to build a boost towards the clutch.
Torque during launch table
Torque control table when the digital input launch control is active. This is the torque (in Nm) which is transmitted to the TCU during launch. As soon as the launch button is released, the regular torque control tables is used.
Note: A value between -600 and -1024 is necessary to not burn the clutches during the building of boost.
Burnout rpm table
To be able to do a burnout with the DCT gearbox, you might need to activate the digital input DCT clutchkick/burnout mode to force a negative torque value to be sent to the TCU during engine rev-up (no clutch engagement), when exceeding this RPM value, MaxxECU rapidly transmitting FULL torque to simulate a clutchkick to make the wheel spin and make sure no clutch slippage during the burnout.
torque value before burnout RPM
The reported torque (Nm) until burnout RPM is reached (WHILE the digital input DCT clutchkick/burnout mode is active). (default -500Nm).
used toRQUE mode after burnout RPM reached
•use max torque available - Uses the max value available in this configuration, max value set in DCT Settings, max reported torque value (min/max) when the burnout input is active.
•Use regular torque table - Uses the regular torque table values when the burnout input is active.
Possible to make a burnout with MaxxECU controlling the DCT gearbox? Yes...
DO NOT TRANSMIT MORE TORQUE THAN YOUR ENGINE DELIVERS, YOU WILL GET TCU ADAPTION ERROR CODES AND WEIRD SHIFTS
DCT torque
This is the main torque table, transmitting the torque value to the TCU, as written above, the transmitted torque value has a direct relation to clutch pressures.
Example torque values:
•Idle: -100 to 50Nm, keep it as low as possible to prevent vehicle from moving without having the brake pedal engaged, to high number on idle will give TCU error codes.
•Light load: try to keep the value as low as possible, without having to much clutch slip.
•Middle load: Same here, do not send to much torque, it will give you "rough" shifting operation, but must be high enough to prevent too much clutch slippage.
•High load: Be sure not to send to much torque before the engine actually has almost the same torque load.
Note: If the transmitted torque value differs to much from the calculated clutch torque (inside the TCU), a DCT error code will be thrown and shifting operations will go sideways.
1. Example Torque table, in this example our engine is turbocharged which means it is not advisable to have the pedal as it load axis.
2. Set up a user table with Throttle position (which is our pedal in our system when E-Throttle is activated) as the load axis. For speed axis, select MAP as the source. Tune accordingly.
In the above example, the output value of this user table will reflect both TPS and MAP, but limited to 0 to 100%
Note: The same could be done on for example the main fuel table...
3. Drive around (preferable on a dyno where you can see actual engine torque and populate the torque table with as close to real values as you can think of).
•Less Torque --> Will increase the clutch slip.
•To much torque --> Will shift too hard.
Note for GEN1: One small tip is to drive around and change the table values while looking at BMW INPA diagnostic tool calculated clutch torque values in realtime.
|
DCT reported throttle angle
Table used to alter the reported throttle angle to the DCT TCU. Can be used to adjust the shift points in automode.
Note: Not used with the default shifting strategy.
DCT torque correction
The torque correction table, mostly used during launch to make a small clutch slip to prevent wheels from slipping.
100% = no correction (normal and standard value) = uses the main torque table.
Note: Be careful here, especially with a lot of power, not to let the DCT clutches slip for a longer period of time, see DCT hardware upgrade.
DCT shifting options
DCT UP shift
Shiftcut on UP shift is not "needed", it works flawlessly without any kind of cut, but might increase the ware of your clutches, but it shifts fine without....your decision.
Note: The shiftcut event is ALWAYS triggered from the DCT control to the shiftcut system during an up shift event, regardless of Drivelogic mode, engine load or pedal position, it is up to the Shiftcut settings to decide whether to do a shiftcut or not.
The above image is an example of how the different signals MaxxECU is received during an up shift event from a M3 TCU, and also how it should look like!
1. The shift signal is received (Green).
2. Gear indication (Blue) will increment during the up shift event.
3. The Torque reduction signal sends a signal to the MaxxECU indicating to lower engine torque (shiftcut) during the shift operation.
How to determine the Shiftcut source
Multiple torque reduction signals in one single shift operation
If you get the above, several torque reduction signals during one single up shift event, you cannot use torque request from tcu as the shiftcut source. You have to use shift signal from tcu as shiftcut source.
Lack of torque reduction signal randomly
In the above example, we get a very short, or not even an Torque reduction Request signal at all, in the above case, you must use shift signal from tcu as shiftcut source.
Note: it is always safest to use the Shift signal from TCU.
Example shiftcut delay time when using the shiftcut signal from TCU as shiftcut source.
Note: If using the Shift signal from TCU as shiftcut source, an shift cut delay of around 0.020(20ms) to 0.040sek(40ms) is necessary to make torque reduction at the correct time.
|
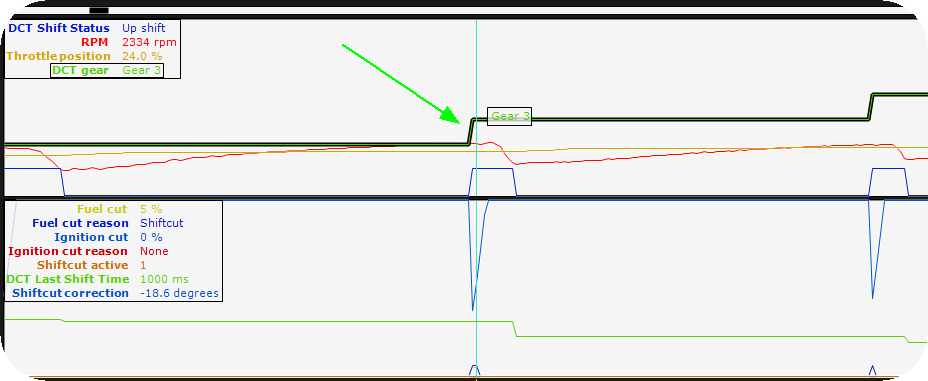
Example interesting data during an DCT up shift operation, with shiftcut feature activated.
Example shiftcut setting, here different settings for up and down shifts using the True 4D feature of MaxxECU. See DCT shifting options for all shifting options.
The above image is an example of how the different signals MaxxECU is received during an up shift event from a M3 TCU, and also how it should look like!
1. The shift signal is received (Green).
2. Gear indication (Blue) will increment during the up shift event.
3. The Torque reduction signal sends a signal to the MaxxECU indicating to lower engine torque (shiftcut) during the shift operation.
How to determine the Shiftcut source
Multiple torque reduction signals in one single shift operation
If you get the above, several torque reduction signals during one single up shift event, you cannot use torque request from tcu as the shiftcut source. You have to use shift signal from tcu as shiftcut source.
Lack of torque reduction signal randomly
In the above example, we get a very short, or not even an Torque reduction Request signal at all, in the above case, you must use shift signal from tcu as shiftcut source.
Note: it is always safest to use the Shift signal from TCU.
Example shiftcut delay time when using the shiftcut signal from TCU as shiftcut source.
Note: If using the Shift signal from TCU as shiftcut source, an shift cut delay of around 0.020(20ms) to 0.040sek(40ms) is necessary to make torque reduction at the correct time.
|
How to DCT downshift (GEN1 drivelogic mode 1,2,3 / GEN2 drivelogic mode 1)
The TCU sends an downshift event to MaxxECU (via CAN) which internally activates the Throttle blip feature, which is a required to successfully downshift in this mode.
Downshift with pedal below 2%.
Just press the downshift, and it will downshift :)
Note: The shiftcut event is NOT triggered below 2% pedal in ANY drivelogic mode.
DCT downshift with pedal over 2%.
Over 2% pedal, the torque table is used, and in some cases it MIGHT need to use the shiftcut feature to reduce engine power during a downshift.
Note: The shiftcut event IS always triggered over 2% pedal position in ANY drivelogic mode.
Note: The shiftcut event is always triggered when there is an down shift event from the DCT, when pedal is over 2% position.
1. Do some basic Shiftcut setting.
2. Change the axis of the Shiftcut time table to suit your need. These shiftcut time table will always be used, regardless of an up shift or an down shift event.
3. Right click anywhere on the table, select 4D Axis --> Add 4D axis. True 4D is explained here.
4. Right click on the 4D axis table, select Change axis source and change to the DCT Shifter Status available under DCT Trans.
5. Rescale like the above.
Note: DCT Shift Status, 1 = SHIFT_UP, 2 = SHIFT_DOWN.
6. If you have done everything correctly, it will look something like this, which means up shift and down shift have different shiftcut time tables.
7. Add 4D axis on Retard angle to have a different ignition retard on up and down shift (if needed, that depends on your application). Change to suit your need.
8. Add a 4D axis to the ignition and fuel drop tables, the above shows example of drop tables for an up shift.
9. Example drop tables on a down shift.
Note: We have seen that just a little power reduction during a downshift, will increase the shift speed, cause the TCU needs to "detect" some reduced power during this shift operation.
|
How to DCT downshift and throttle blip (GEN1 drivelogic mode 4,5,6 / SPORT MODE / GEN2 drivelogic 3)
Downshift with pedal below 2% (blip is required)
The TCU sends an downshift event to MaxxECU (via CAN) which internally activates the Throttle blip feature, which is a required to successfully downshift in this mode.
Note: The shiftcut event is NOT triggered below 2% pedal in ANY drivelogic mode.
Note: Before you are trying to setup blip, we assume a valid DCT torque table is tuned in DCT Control and that up shifting is working properly.
1. In DCT settings, blip delay, set a default blip delay of 60ms blip delay (as a starting point).
Note: Values below 40ms might make the system react strangely. Over 80ms it might throw out the gear and go into idle rpm.
2. In Motorsport --> Throttle blip, set basic settings. The above might be a good starting point. Depending on engine size and response it requires different blip time and throttle targets, individually by gear and RPM.
3. The TCU calculates a requested "Blip Target engine RPM" right before the blip event is triggered, this value can be seen in the logger (DCT Blip Target RPM). You need to make your blip settings so that the engine RPM gets right above this the blip target RPM, from our experience it is better to have a too high engine RPM than the actual target blip RPM to make sure the TCU wont disengage the clutches. Also pay attention to the DCT last shift time, when over 1500ms, it is most likely there is something wrong.
NOTE: DCT BLIP TARGET RPM is NOT available for the GEN2 protocol.
By watching the clutch slip (%) during a shift operation, which should look like the above, all is good.
Here we can see a clear example of that the TCU is unhappy with our blip settings, in the above example we did not achieve the wanted engine RPM, and therefore the TCU disengages the clutches and the shift operation took a very long time to be completed.
|
DCT downshift with pedal over 2%.
Over 2% pedal, the torque table is used, and in some cases it MIGHT need to use the shiftcut feature to reduce engine power during a downshift.
Note: The shiftcut event IS always triggered over 2% pedal position in ANY drivelogic mode.
Note: The shiftcut event is always triggered when there is an down shift event from the DCT, when pedal is over 2% position.
1. Do some basic Shiftcut setting.
2. Change the axis of the Shiftcut time table to suit your need. These shiftcut time table will always be used, regardless of an up shift or an down shift event.
3. Right click anywhere on the table, select 4D Axis --> Add 4D axis. True 4D is explained here.
4. Right click on the 4D axis table, select Change axis source and change to the DCT Shifter Status available under DCT Trans.
5. Rescale like the above.
Note: DCT Shift Status, 1 = SHIFT_UP, 2 = SHIFT_DOWN.
6. If you have done everything correctly, it will look something like this, which means up shift and down shift have different shiftcut time tables.
7. Add 4D axis on Retard angle to have a different ignition retard on up and down shift (if needed, that depends on your application). Change to suit your need.
8. Add a 4D axis to the ignition and fuel drop tables, the above shows example of drop tables for an up shift.
9. Example drop tables on a down shift.
Note: We have seen that just a little power reduction during a downshift, will increase the shift speed, cause the TCU needs to "detect" some reduced power during this shift operation.
|