BMW DCT related links
•BMW DCT BIG HOWTO. <-- READ this guide, please, just do it before asking questions already covered.
•BMW DCT error codes.
•BMW DCT TCU firmware flashing.
•BMW DCT CAN protocol.
•BMW INPA diagnostic tool.
•DCT clutch relearn.
•DCT hardware identifier
•DCT hardware upgrade.
•BMW installation and wiring.
•DCT shifter emulation.
•DCT Realtime Data description.
•DCT shifting options.
•MTune - DCT Control.
•MTune - DCT Settings.
Gearbox type
Specifies the gearbox type and the TCU (Transmission Control Unit) used. The actual TCU version is the most important thing here.
•GEN1 GS7D36SG DCT (BMW 335 TCU) - OE TCU firmware seems to work.
•GEN1 GS7D36SG DCT (BMW M3 TCU, GTS fw) - GTS based firmware is required.
•GEN2 GS7D36SG DCT (BMW M4 TCU, custom fw) - Custom TCU firmware is required, available using the xHP app, see BMW DCT TCU firmware flashing.
Shifter type
Specifies which gear shifter is used.
•OEM BMW shifter - with this option, stock shifter, SPORT button (BMW 335) or drivelogic button (BMW M3) must be present and communicate directly with the TCU.
•Shifter emulation - with this option, digital inputs are used to "simulate" the OE shifter, DCT shifter emulation.
TCU speed source
The vehicle speed source we report to the TCU.
•Vehicle speed (using TCU OEM rear end diff ratio) - Can ONLY be used when your rear end diff ratio is2.65 (GEN1 335), 3.15 (GEN1 M3) and 3.46 (GEN2 M4).
•Undriven wheel speed (rear end diff ratio setting - corr) - Uses the correct vehicle speed (undriven) and your rear end diff ratio (and using the below Speed gear ratio correction (to TCU) correction) to calculate a correct TCU speed value.
•Driven wheel speed (rear end diff ratio setting - corr) - Uses the correct vehicle speed (driven) and your rear end diff ratio (and using the below Speed gear ratio correction (to TCU) correction) to calculate a correct TCU speed value.
•Undriven & Driven wheel speeds (rear end diff ratio setting - corr) - Uses the correct vehicle speed (undriven and driven) and your rear end diff ratio (and using the below Speed gear ratio correction (to TCU) correction) to calculate a correct TCU speed value.
•Dyno Mode (using rpm & current gear) - corr - Dyno mode, mainly for customers mounted a front wheel speed sensor but heading to a RWD dyno where front wheel not moving. <-- Experimental feature, less perfect shift operation will occur.
Note: The 4 speed values we send to the TCU has a direct relation to shifting points, performance and clutch slippage during shift operations. Therefore the vehicle speed inside MaxxECU must be very precise and accurate, otherwise this will not work.
Speed gear ratio correction (to TCU)
Used to adjust the reported speed to the TCU.
Note: The below REQUIRES that your speed values in MaxxECU is correctly setup, also correct wheel dimensions NEEDS to be accurate before this correction step should take place.
1. Add the Driveshaft RPM and DCT Calculated Driveshaft Speed to your Live-logger.
2. Adjust the speed gear ratio correction value until your Driveshaft RPM and DCT Calculated Driveshaft Speed are as close as possible to each other.
3. You can verify that the DCT reported speed values with MaxxECU speed values.
Note: They SHOULD differ when there is a correction applied.
|
clutch kick time
Specifies the clutch kick time.
•switch input (while input active) - Activates the clutch kick feature (releases the pressure on the clutch in gearbox) while the digital input DCT clutchkick/burnout mode is active.
NOTE: Experimental feature for testings only, you might wanna combine this with a secondary rev limit.
Max reported torque value (min/max)
Modifies the reported (and transmitted) torque value to the TCU with this value in both directions. For example, "800" will limit torque values between -800Nm and 800Nm.
shift strategy
Which shifting strategy to use.
•Default (GEN1/GEN2) - The default shift strategy.
•Improved (BETA) (GEN1 only) - This is the TEST mode for the shifting strategy which includes our latest changes and fixes.
Note: The shiftcut signal is always triggered upon an UP or DOWN shift event (signaled from the TCU), you need to set them up in MaxxECU Shiftcut settings.
DCT downshift requires everything to be correctly set and a Throttle blip function is required.
Shiftcut source
Note: GEN2 protocol does not use this setting.
Specifies which function to trigger the MaxxECU Shiftcut input.
•torque request from tcu - Uses the torque request input to trigger the internal shiftcut input (preferable use this method).
•shift signal from tcu (recommended) - Uses the shift input (which happends a few milliseconds before the above actual torque request signal) as shiftcut input trigger.
Note: The reason why we have this option, is because we have seen issues with the above Torque request from TCU signal from the TCU in some application (for an unknown reason).
The above image is an example of how the different signals MaxxECU is received during an up shift event from a M3 TCU, and also how it should look like!
1. The shift signal is received (Green).
2. Gear indication (Blue) will increment during the up shift event.
3. The Torque reduction signal sends a signal to the MaxxECU indicating to lower engine torque (shiftcut) during the shift operation.
How to determine the Shiftcut source
Multiple torque reduction signals in one single shift operation
If you get the above, several torque reduction signals during one single up shift event, you cannot use torque request from tcu as the shiftcut source. You have to use shift signal from tcu as shiftcut source.
Lack of torque reduction signal randomly
In the above example, we get a very short, or not even an Torque reduction Request signal at all, in the above case, you must use shift signal from tcu as shiftcut source.
Note: it is always safest to use the Shift signal from TCU.
Example shiftcut delay time when using the shiftcut signal from TCU as shiftcut source.
Note: If using the Shift signal from TCU as shiftcut source, an shift cut delay of around 0.020(20ms) to 0.040sek(40ms) is necessary to make torque reduction at the correct time.
|
Blip delay
The TCU sends a "blip request" to the MaxxECU, this setting can delay the blip function to make sure the clutches disengages before the engine is revved up.
Example blip delay of 60ms to make the DCT clutches to be release before Throttle blip activation occurs.
clutch slip engine cut
Specifies whether to protect the gearbox clutches against clutch slippage, it is HIGHLY recommended to have this enabled. It uses the below settings for activation of engine cut, see DCT hardware upgrade for example of damaged clutches if it slip too much...
max clutch slip on load
Specifies the maximum allowed clutch slippage when under "load" (VSS > 30km/h, TPS > 15%, RPM > 2000).
Note: we dont pay attention to the slippage during launch and 1000ms after launch is deactivated.
max clutch slip during shifting
During DCT shiftings, we cant calculate the slip rate accurately, therefore during shifting we allow a higher slippage to prevent unnecessary engine cuts during shifting's.
max allowed upshift time (low load)
Specifies the maximum allowed shifting time (ms) during low load. Below 30% TPS.
max allowed upshift time (normal load)
Specifies the maximum allowed shifting time (ms) during normal load. 30 - 80% TPS.
max allowed upshift time (high load)
Specifies the maximum allowed shifting time (ms) during high load. Over 80% TPS
max allowed downshift time
Specifies the maximum allowed shifting time (ms) during a downshift.
DCT UP shift
Shiftcut on UP shift is not "needed", it works flawlessly without any kind of cut, but might increase the ware of your clutches, but it shifts fine without....your decision.
Note: The shiftcut event is ALWAYS triggered from the DCT control to the shiftcut system during an up shift event, regardless of Drivelogic mode, engine load or pedal position, it is up to the Shiftcut settings to decide whether to do a shiftcut or not.
The above image is an example of how the different signals MaxxECU is received during an up shift event from a M3 TCU, and also how it should look like!
1. The shift signal is received (Green).
2. Gear indication (Blue) will increment during the up shift event.
3. The Torque reduction signal sends a signal to the MaxxECU indicating to lower engine torque (shiftcut) during the shift operation.
How to determine the Shiftcut source
Multiple torque reduction signals in one single shift operation
If you get the above, several torque reduction signals during one single up shift event, you cannot use torque request from tcu as the shiftcut source. You have to use shift signal from tcu as shiftcut source.
Lack of torque reduction signal randomly
In the above example, we get a very short, or not even an Torque reduction Request signal at all, in the above case, you must use shift signal from tcu as shiftcut source.
Note: it is always safest to use the Shift signal from TCU.
Example shiftcut delay time when using the shiftcut signal from TCU as shiftcut source.
Note: If using the Shift signal from TCU as shiftcut source, an shift cut delay of around 0.020(20ms) to 0.040sek(40ms) is necessary to make torque reduction at the correct time.
|
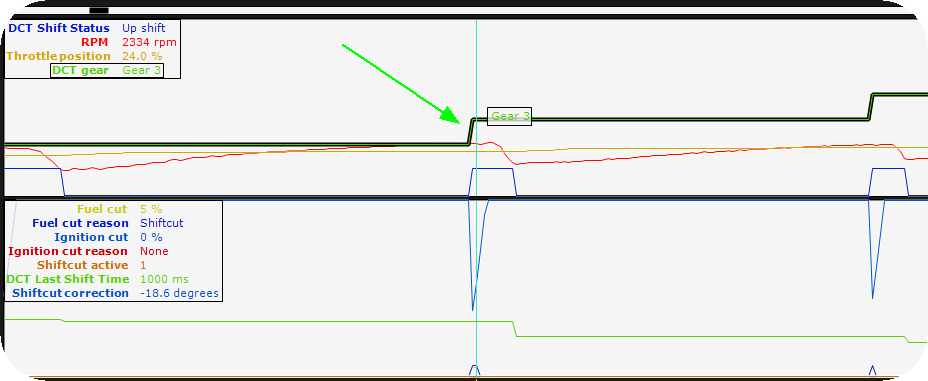
Example interesting data during an DCT up shift operation, with shiftcut feature activated.
Example shiftcut setting, here different settings for up and down shifts using the True 4D feature of MaxxECU. See DCT shifting options for all shifting options.
The above image is an example of how the different signals MaxxECU is received during an up shift event from a M3 TCU, and also how it should look like!
1. The shift signal is received (Green).
2. Gear indication (Blue) will increment during the up shift event.
3. The Torque reduction signal sends a signal to the MaxxECU indicating to lower engine torque (shiftcut) during the shift operation.
How to determine the Shiftcut source
Multiple torque reduction signals in one single shift operation
If you get the above, several torque reduction signals during one single up shift event, you cannot use torque request from tcu as the shiftcut source. You have to use shift signal from tcu as shiftcut source.
Lack of torque reduction signal randomly
In the above example, we get a very short, or not even an Torque reduction Request signal at all, in the above case, you must use shift signal from tcu as shiftcut source.
Note: it is always safest to use the Shift signal from TCU.
Example shiftcut delay time when using the shiftcut signal from TCU as shiftcut source.
Note: If using the Shift signal from TCU as shiftcut source, an shift cut delay of around 0.020(20ms) to 0.040sek(40ms) is necessary to make torque reduction at the correct time.
|
How to DCT downshift (GEN1 drivelogic mode 1,2,3 / GEN2 drivelogic mode 1)
The TCU sends an downshift event to MaxxECU (via CAN) which internally activates the Throttle blip feature, which is a required to successfully downshift in this mode.
Downshift with pedal below 2%.
Just press the downshift, and it will downshift :)
Note: The shiftcut event is NOT triggered below 2% pedal in ANY drivelogic mode.
DCT downshift with pedal over 2%.
Over 2% pedal, the torque table is used, and in some cases it MIGHT need to use the shiftcut feature to reduce engine power during a downshift.
Note: The shiftcut event IS always triggered over 2% pedal position in ANY drivelogic mode.
Note: The shiftcut event is always triggered when there is an down shift event from the DCT, when pedal is over 2% position.
1. Do some basic Shiftcut setting.
2. Change the axis of the Shiftcut time table to suit your need. These shiftcut time table will always be used, regardless of an up shift or an down shift event.
3. Right click anywhere on the table, select 4D Axis --> Add 4D axis. True 4D is explained here.
4. Right click on the 4D axis table, select Change axis source and change to the DCT Shifter Status available under DCT Trans.
5. Rescale like the above.
Note: DCT Shift Status, 1 = SHIFT_UP, 2 = SHIFT_DOWN.
6. If you have done everything correctly, it will look something like this, which means up shift and down shift have different shiftcut time tables.
7. Add 4D axis on Retard angle to have a different ignition retard on up and down shift (if needed, that depends on your application). Change to suit your need.
8. Add a 4D axis to the ignition and fuel drop tables, the above shows example of drop tables for an up shift.
9. Example drop tables on a down shift.
Note: We have seen that just a little power reduction during a downshift, will increase the shift speed, cause the TCU needs to "detect" some reduced power during this shift operation.
|
How to DCT downshift and throttle blip (GEN1 drivelogic mode 4,5,6 / SPORT MODE / GEN2 drivelogic 3)
Downshift with pedal below 2% (blip is required)
The TCU sends an downshift event to MaxxECU (via CAN) which internally activates the Throttle blip feature, which is a required to successfully downshift in this mode.
Note: The shiftcut event is NOT triggered below 2% pedal in ANY drivelogic mode.
Note: Before you are trying to setup blip, we assume a valid DCT torque table is tuned in DCT Control and that up shifting is working properly.
1. In DCT settings, blip delay, set a default blip delay of 60ms blip delay (as a starting point).
Note: Values below 40ms might make the system react strangely. Over 80ms it might throw out the gear and go into idle rpm.
2. In Motorsport --> Throttle blip, set basic settings. The above might be a good starting point. Depending on engine size and response it requires different blip time and throttle targets, individually by gear and RPM.
3. The TCU calculates a requested "Blip Target engine RPM" right before the blip event is triggered, this value can be seen in the logger (DCT Blip Target RPM). You need to make your blip settings so that the engine RPM gets right above this the blip target RPM, from our experience it is better to have a too high engine RPM than the actual target blip RPM to make sure the TCU wont disengage the clutches. Also pay attention to the DCT last shift time, when over 1500ms, it is most likely there is something wrong.
NOTE: DCT BLIP TARGET RPM is NOT available for the GEN2 protocol.
By watching the clutch slip (%) during a shift operation, which should look like the above, all is good.
Here we can see a clear example of that the TCU is unhappy with our blip settings, in the above example we did not achieve the wanted engine RPM, and therefore the TCU disengages the clutches and the shift operation took a very long time to be completed.
|
DCT downshift with pedal over 2%.
Over 2% pedal, the torque table is used, and in some cases it MIGHT need to use the shiftcut feature to reduce engine power during a downshift.
Note: The shiftcut event IS always triggered over 2% pedal position in ANY drivelogic mode.
Note: The shiftcut event is always triggered when there is an down shift event from the DCT, when pedal is over 2% position.
1. Do some basic Shiftcut setting.
2. Change the axis of the Shiftcut time table to suit your need. These shiftcut time table will always be used, regardless of an up shift or an down shift event.
3. Right click anywhere on the table, select 4D Axis --> Add 4D axis. True 4D is explained here.
4. Right click on the 4D axis table, select Change axis source and change to the DCT Shifter Status available under DCT Trans.
5. Rescale like the above.
Note: DCT Shift Status, 1 = SHIFT_UP, 2 = SHIFT_DOWN.
6. If you have done everything correctly, it will look something like this, which means up shift and down shift have different shiftcut time tables.
7. Add 4D axis on Retard angle to have a different ignition retard on up and down shift (if needed, that depends on your application). Change to suit your need.
8. Add a 4D axis to the ignition and fuel drop tables, the above shows example of drop tables for an up shift.
9. Example drop tables on a down shift.
Note: We have seen that just a little power reduction during a downshift, will increase the shift speed, cause the TCU needs to "detect" some reduced power during this shift operation.
|
TCU diagnostic requests
When enabled, MaxxECU are requesting TCU diagnostic values to get individual clutch pressures, calculated torque and line pressure.
Note: INPA cannot communicate with the TCU while this is enabled.
Reset TCU adaptations
This button resets:
•Adaptation values of clutch torque characteristic K1.
•Adaptation values of clutch torque characteristic K2.
•Adaptation values for DRM.
•Adaptation values of the semi-slip for gears 1-7.
Note: we are NOT resetting: Adaptation values Kisspoint K1/K2.